前半では、一般的なポケット加工の荒取りを中心に取り上げ、後半で、負荷制御の加工方法について取り上げています。
切削距離(L)の計算では、HSMWorks で実際に CAM で計算した距離を使いました。
↑top
底刃加工 と 側面刃加工 の基本的な違い
例として、10 x 10 x 10 の立方体に φ3エンドミルで切削加工して、3 x 3 の切り欠きを作ります。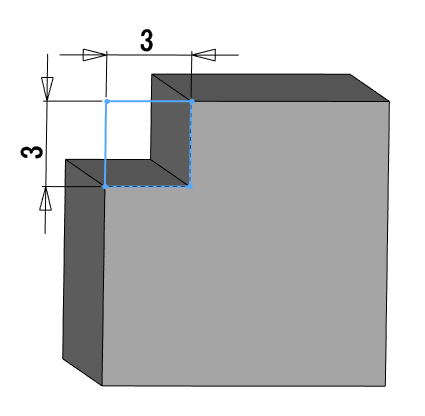
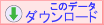
主に底刃を使った加工 と 主に側面刃を使った加工を考えます。
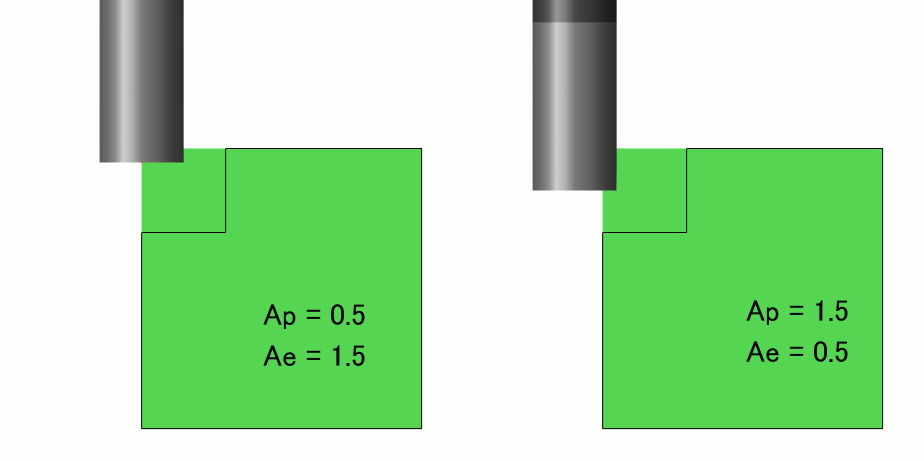
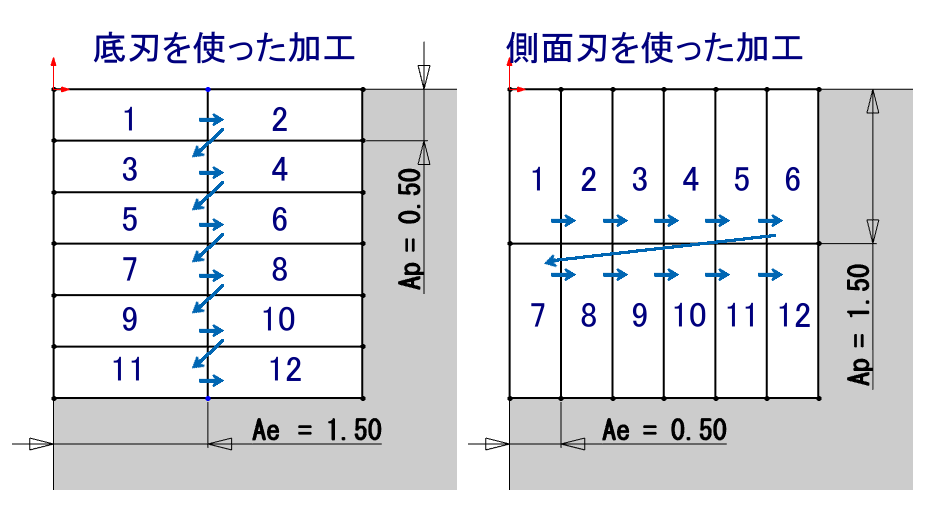
Ap X Ae が等しい場合、
どちらも 12回の切削で加工され、切削距離は ほとんど等しくなります。
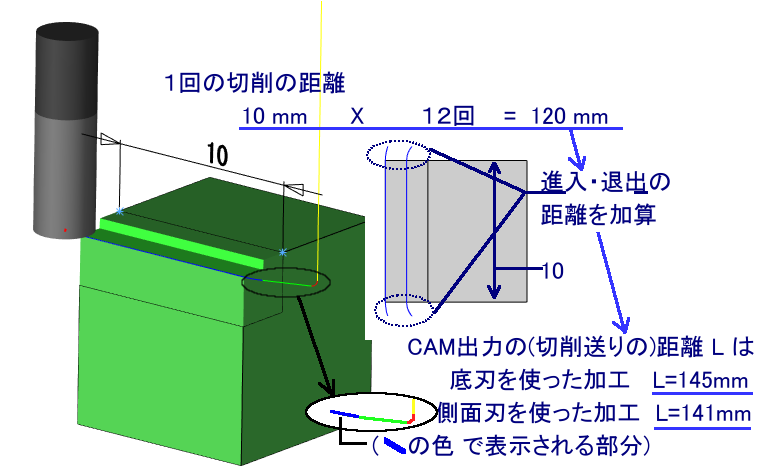
上の図はポケット加工ですが、これは負荷制御でも同様です。
ここで分かることは、Ap X Ae が等しければ、底刃 と 側面刃の切削距離は ほとんど同じで、進入退出部分の距離の違いがあることです。
↑top
溝加工
今度は、φ2エンドミルで、 同様開いた形状と 溝切削の形状の加工を比較します。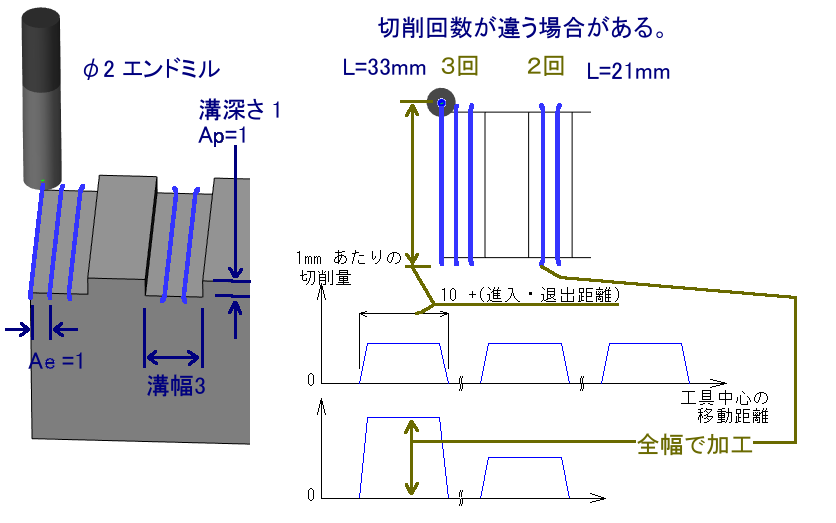
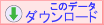
上図のように、通常のポケット加工では Ae =1 を指示しても全幅で加工する場合があります。
その場合、負荷(グラフの縦軸=1mmあたりの切削量)が約2倍となります。
そして、切削回数が少なくなり、切削距離が短くなります。 ↑top
止まり溝(コーナーのR)
通常のポケット加工の場合、溝の片端、または両端が "止まり"の場合、切削距離は短くなります。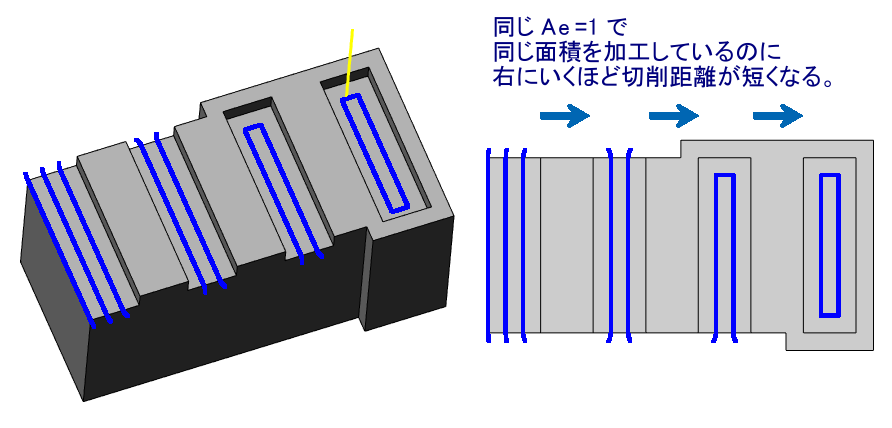
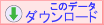
短くなった分だけ、"止まり" のコーナーで負荷(1mm あたりの切削量)は、大きくなります。
次の右側2個のように内側Rでは、実際の工具負荷 w は 指示した Ae より大きな負荷となります。
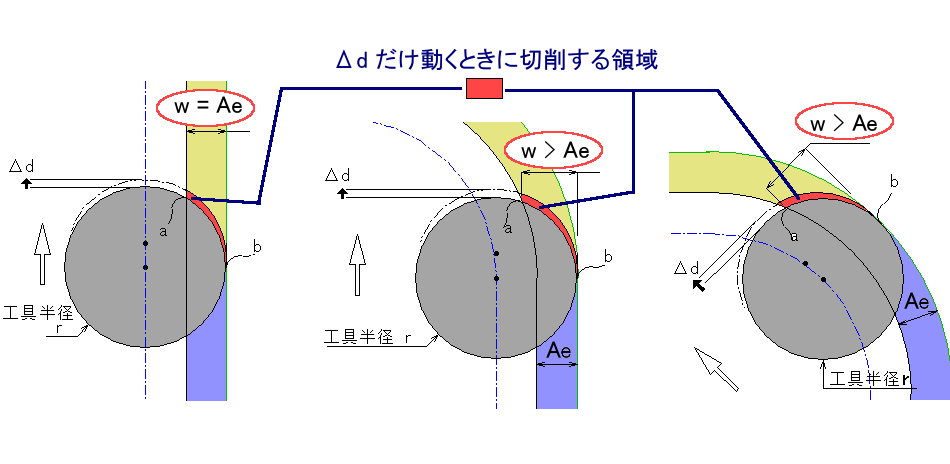
内側Rの半径が小さい場合や 鋭角のコーナーの場合は、次のように工具の全幅の負荷がかります。
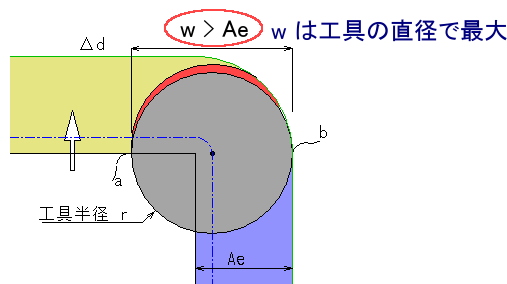
↑top
負荷制御のピッチ
HSMWorks 開発メーカーでは、負荷制御の加工方法について
「工具負荷の最大値を保証する」 (guarantee a maximum tool load)
と述べていて、CAM では その最大値を「最適負荷 (Optimal Load)」という欄に入力します。
しかし、何を工具負荷とみなすのか、実際の工具負荷は加工中どう変化するのか、についての詳細は述べられていません。
ここでは、実際に出力されるツールパスから その詳細を推測しています。
(記述が一部間違いがありましたので訂正しました。2014-01-26)
しかし、何を工具負荷とみなすのか、実際の工具負荷は加工中どう変化するのか、についての詳細は述べられていません。
ここでは、実際に出力されるツールパスから その詳細を推測しています。
(記述が一部間違いがありましたので訂正しました。2014-01-26)
負荷制御では、直線を加工した場合の XYピッチ(Ae)に相当する値を「最適負荷」に指示します。
その値が w の最大値となります。
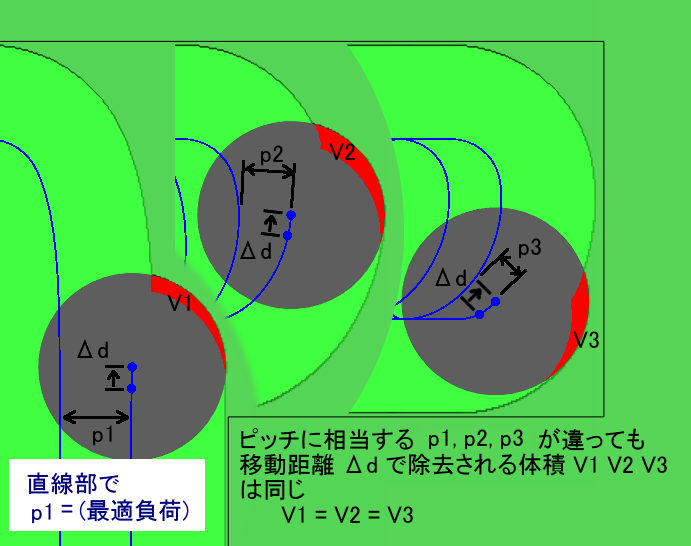
直線部のピッチ p1 は Ae に等しくなりますが、
それ以外の場所では、上図の赤の部分の面積(V1,V2,V3)が同じになるように
p2,p3 の値が小さく調整されます。
通常のポケット加工と 負荷制御の実際に出力されたパスの切削距離を調べてみました。
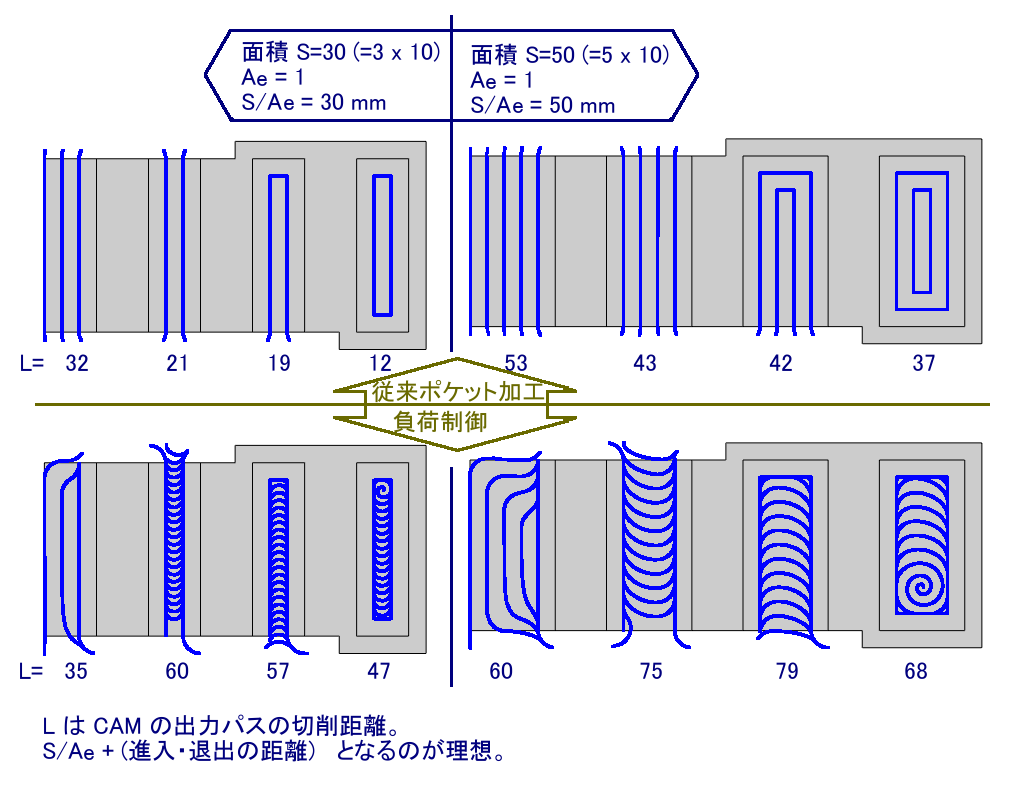
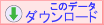
面積 S を XYピッチ Ae で割った値 (S/Ae) は、 もし全領域で一定の負荷(1mm あたりの切削量)で切削できるとした場合の 切削距離です。
実際には進入・退出のときに 負荷が小さくなりますので、その分だけ切削距離は長くなります。
従来ポケット加工では S/Ae より小さくなっていて、負荷が大きい部分があることがわかります。
↑top
進入・退出の負荷
進入・退出のとき w は、指定した Ae より小さくなります。下図はそのイメージ図です。
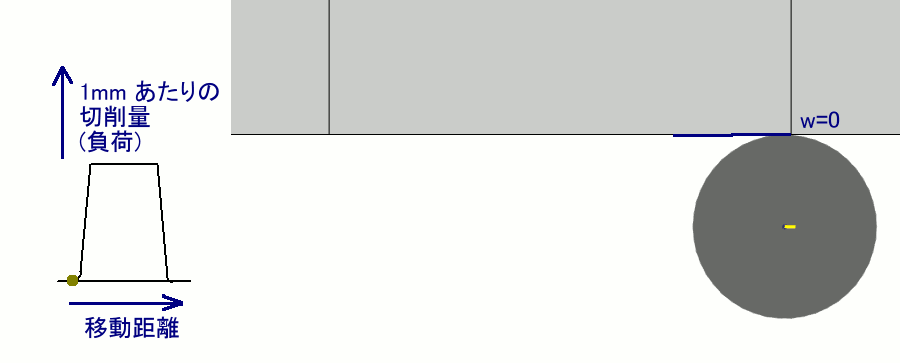
進入・退出の箇所が多いほど、w < Ae となる箇所が多くなります。
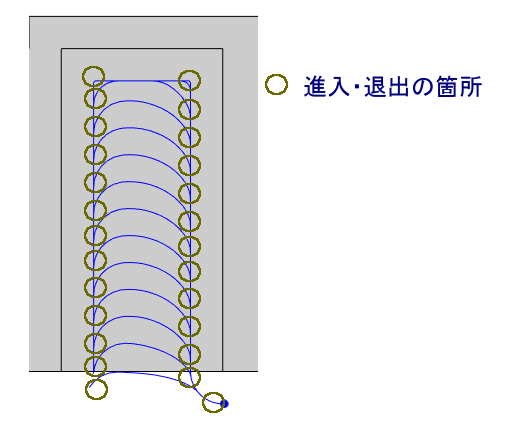
形状が左右対称であっても、進入箇所 と 退出箇所 では負荷が違いますので対称でありません。
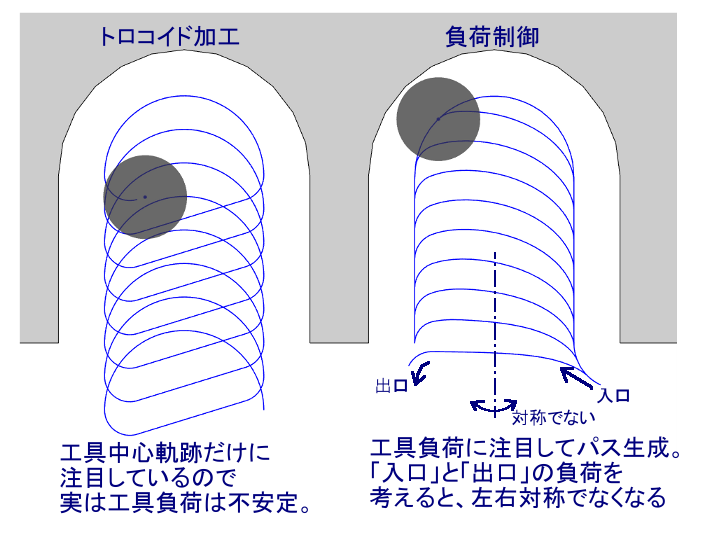
↑top
切削送り以外の移動
ここまでは、「切削送り」で工具が移動する距離だけに注目しました。実際には、退出した後 次の進入位置まで移動する必要があります。
HSMWorks では、送り速度を「切削送り」、「進入送り」「退出送り」などを最適に指定することができます。
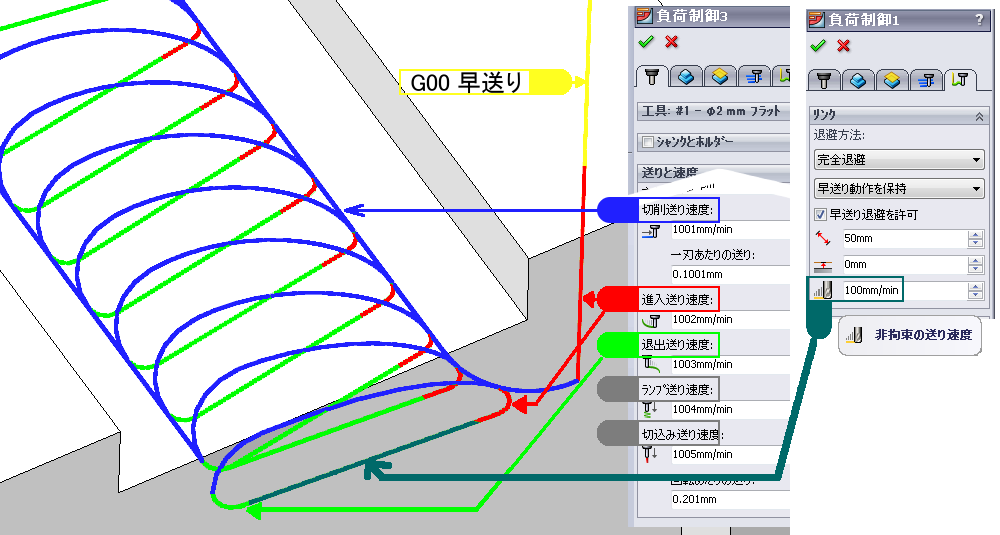
負荷制御パスでは、「退出送り」を速くすることで時間を節約できます。
また、リフト高さは、負荷のない移動の高さを制御できます。
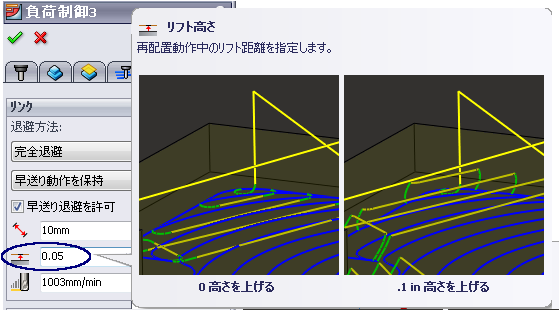